3D Scanning Used to Meet Bonneville Salt Flats Racing Requirement to Attempt Land Speed Record
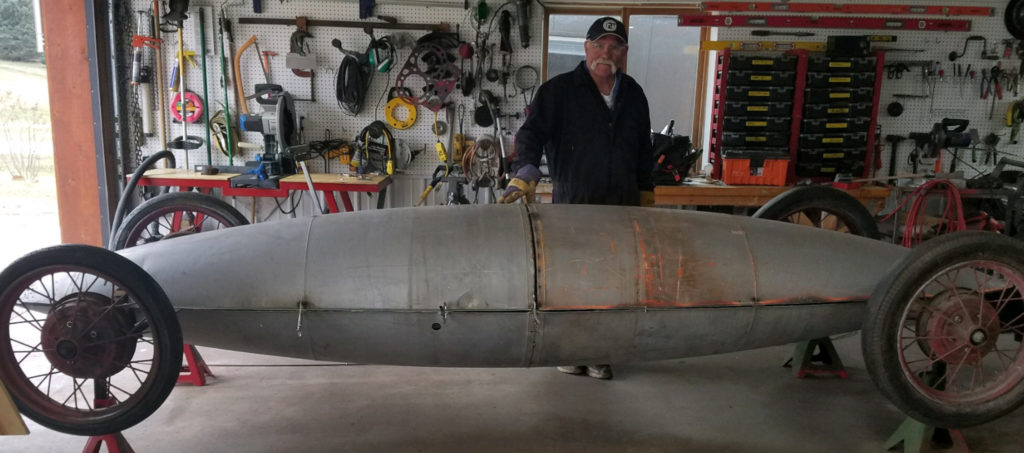
Bob Degezelle with the Belly Tank Race Car
Project
When Bob Degezelle retired as superintendent in the construction industry, he needed a “full-time” project to support his passions in engineering, speed, and adventure. As a lifelong motorhead, Bob chose to focus his time on creating a belly tank race car that would attempt to break the associated land speed record at the Bonneville Salt Flats Speedway.
To accomplish this goal, Bob acquired an old fuel tank from an older-generation bomber style aircraft, which he used to create a special car body shape after cutting and welding the tank to reduce its size. Upon further research and engineering, Bob then modified a Ford Model A engine and adapted a Chevrolet transmission and supporting drivetrain components to a custom-built frame that supported the body and powertrain of this terrific tanker. Next, he integrated tailor-made wheels that had been rotated, ground and optimized for the exact racing scenario that he would see at the salt flats. The final step was to ensure safety of the driver and adherence to the car design requirements from the racing association. Bob needed a roll cage!
Challenge
One of the most unique and interesting parts about a belly tank racer is that the body is made from a modified underwing fuel tank from an older-generation bomber style aircraft. While this racer-from-scraps project sounds like a child’s daydream, this project exists in reality, and the engineering and design work need to be highly sophisticated to achieve desired performance while making sure the car is safe.
One aspect of the safety requirements of the car design is that a roll cage be built and installed that meets certain specifications for roll bar diameter and wall thickness along with approved mounting to the frame. Now that Bob has created a one-of-a-kind body shape with custom powertrain to fit inside, he is left with a monumental measurement challenge to enable the best roll cage design possible that his traditional tools will not solve. Not only does the roll cage need to be sturdy and secure, but it also needs to fit among a modified engine and powertrain components that have already been built into the race car, while providing enough room for a driver to operate this “fuel tank on wheels” up to speeds of over 150 MPH.
Results
Luckily, Bob’s son, who works in engineering, told him about a technology that may be able to provide the 3D measurement solution Bob needed to complete his project – 3D scanning. Bob searched the internet and found Laser Design, a group of highly skilled and experienced resources that offer 3D scanning services both in-lab, at their Minneapolis-based facility, and onsite throughout the US at their customer’s facilities. As a first step, Laser Design’s sales engineer needed to learn the specifics of Bob’s application including location, timing, measurement requirements, use of final deliverables, etc. After a conversation on the phone, much of which was spent learning about belly tank racing and the exciting project Bob had embarked on, it was clear that 3D scanning, and the services offered by Laser Design, would be a perfect fit for Bob based on the following challenges:
- Deliverable:
- Bob would need an accurate 3D CAD model of the body shape of his tanker design, along with the frame and axles, to provide to his roll cage designer for digital modeling of the design and fabrication of the physical cage.
- Location:
- The 3D scanning would need to take place onsite at his location.
- Speed:
- The 3D scanning and CAD modeling work needed to be completed as quickly as possible in order to support a tight schedule and be prepared for a meeting with a racing official to review the design and project requirements.
Solution
Laser Design was able to provide Bob with an experienced onsite 3D scanning technician, equipped with an Artec Leo portable and handheld 3D scanner for the data collection process. Critical measurements included the external car body shape from the customized tank design, along with frame and axle dimensions available after removing the top half of the body. The Artec Leo was the perfect 3D scanning device as it is extremely fast, easy to operate, and highly portable for this application. The Artec Leo allowed Laser Design to capture and verify all 3D measurements within a couple hours after arriving onsite at Bob’s facility.
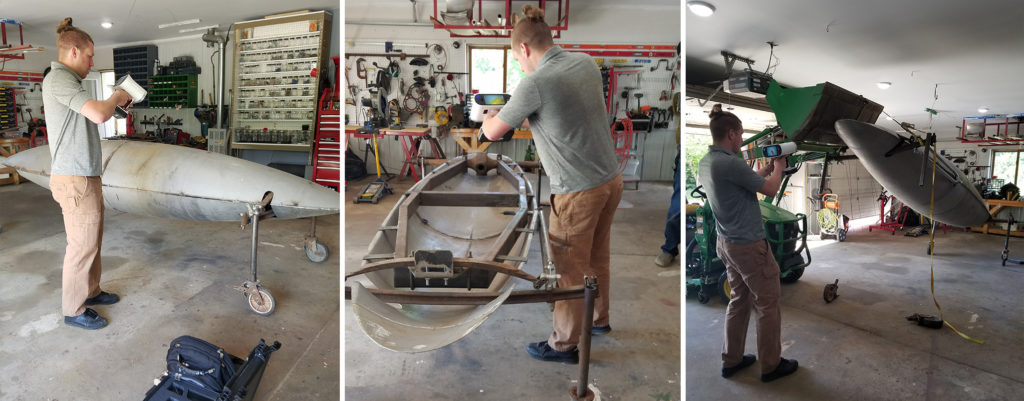
Laser Design Scanning Technician using handheld Artec Leo to scan the top, inside, and bottom of the race car body and frame.
This data was then used to create and deliver a design-intent 3D CAD model assembly in .STP (.stp or .step) format, allowing the 3D CAD designer to create and optimize the shape of the roll cage within SOLIDWORKS to fit snugly in the body and mount to the proper locations of the frame. All work was scheduled and completed within 2 weeks of Bob’s initial call to Laser Design.
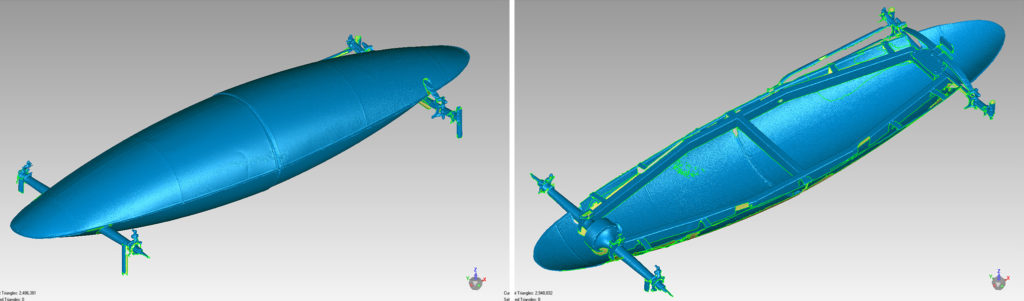
Exterior and Interior Scan Data of Body and Frame
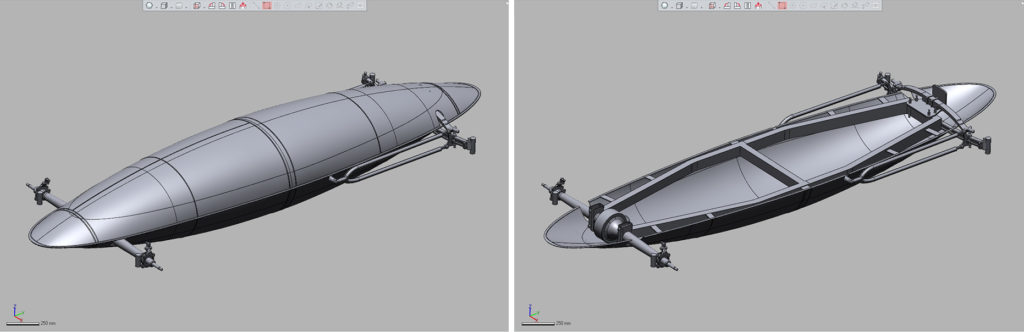
CAD model of Exterior and Interior of Body and Frame
Summary
The aerodynamic shape and large size of underwing fuel tanks used during and after WWII make them ideal for modification into race car body designs that are used to break land speed records. Once the basic shape of the one-of-a-kind belly tank racer is created, 3D scanning technology can be used to measure the physical geometry and allow for design and creation of a custom fitting roll cage into the assembly. Laser Design has been providing 3D scanning services to individuals and companies in all industries looking for fast and accurate 3D measurements, along with the right 3D CAD model deliverables for over 30 years. We are happy to have met Bob through this project and excited that we are able to help him pursue his new “full-time” job of designing a car that will give him the chance to break World Records. We will continue to follow Bob’s adventure and update with details as he finalizes his design and heads to Bonneville.