Artec Space Spider 3D Scanner and ANSYS® SpaceClaim® direct modeling software optimize fixture design process for high speed CyberOptics SQ3000™ CMM valve body inspection application.
Project
Slow, costly and inflexible are words that have been heard over and over when discussing the creation of inspection fixtures used to measure parts and assemblies with coordinate measurement machines (CMM’s), vision systems and manual inspection processes. Dedicated fixtures are often required for applications that require precise mounting surfaces and datum features while rigidly supporting parts for reliable and repeatable measurements. Traditional approaches to fixture creation include CNC machining, a subtractive process of removing material from a blank, or building the desired shapes and features using modular kits. Both techniques have their issues as machining fixtures can be time consuming and expensive while modular setup can be tedious and inaccurate.
One of our customers recently searched for a high-speed solution for a challenging inspection of their valve bodies to measure flatness, slot width, feature shape, and other critical inspection points. After reviewing modern 3D scanning technologies and what is on the horizon, they identified CyberOptics’ proprietary SQ3000™ CMM with Multi-Reflection Suppression™ (MRS™) sensor technology, that provides highly accurate inspection and measurements in just seconds, as a near perfect-fit for their inspection needs. However, they still required an equally fast and effective solution to generate the necessary fixtures that hold the part during the inspection process.
Challenges
In today’s manufacturing environment, time is money, and inspection is not considered a value-added step in the process even though it is extremely important and required to ensure parts and assemblies meet advertised performance and specifications. This customer has already identified the SQ3000™ CMM technology that will help reduce time to measure, inspect and report critical form and dimensional information, but they’ve been struggling with identifying the most efficient way to reduce time spent on inspection setup processes. Primarily, they are focused on eliminating unnecessary and time-consuming steps from the fixture development process, while allowing their key team members and resources, which include 3D CAD designers, machine operators and CNC machining centers, to focus on critical path items that support value added operations.
Results
Once the customer’s pain points and goals were communicated to Laser Design team members, it became clear very quickly that we could support this customer with easy to use and efficient tools that could be used by their employees that are not part of critical path operations.
The solution offered by Laser Design included the following items:
- Artec Space Spider 3D scanner
- ANSYS SpaceClaim direct modeling software
- Use of customer’s existing 3D printing system
The Artec Space Spider 3D scanner provides a fast, easy to use and accurate way to capture 3D measurements of many objects. The 3D scan data can then be used with ANSYS SpaceClaim direct modeling software, to create simple but effective fixture geometry that can then be sent to a 3D printer for additive manufacturing process. Below is a summary of the process and timing needed for this project.
3D Scan, Fixture Design and 3D Print Process:
Capture
Capture 3D scan data of valve body using Artec Space Spider 3D Scanner. Import Data into ANSYS SpaceClaim direct modeling software (STL format mesh file from Artec Studio software).
– Time: 1 hour
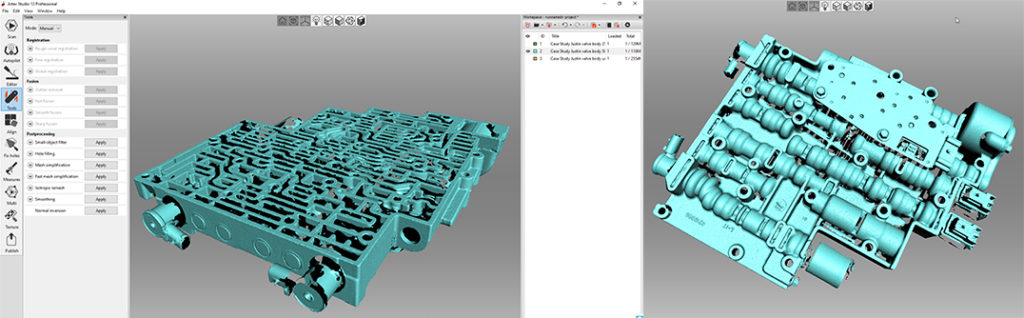
Scan Data in Artec Studio Software
Create
Create fixture design with easy to use pull, move, fill and combine tools. Export mesh to use for 3D printing (STL from ANSYS SpaceClaim).
– Time: 2 hours
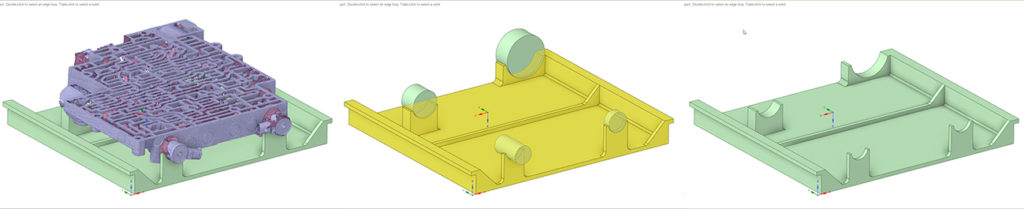
(Left) Valve body STL mesh with fixture design; (Center) Fixture design with features; (Right) Fixture design for 3D printing
3D Print
Setup and 3D Print Fixture
– Time: Fixture print timing of 14 hours (other printers will vary)
Mount part and use for SQ3000 CMM inspection
– Time: under 1 minute to inspect valve body on SQ3000 CMM
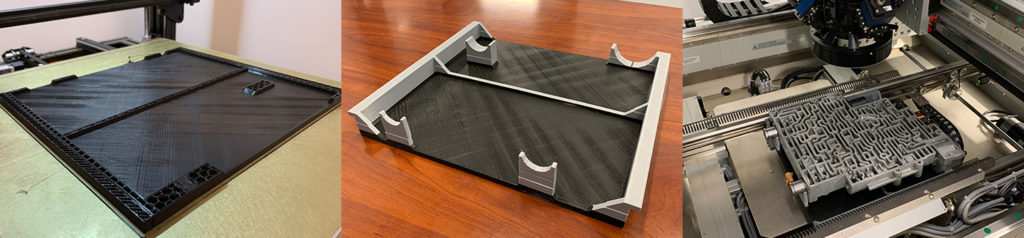
(Left) Base of 3D printed fixture; (Center) Completed 3D print of Fixture; (Right) Valve body mounted in fixture and in the SQ3000 system
Overall Timing for Custom Fixture Design and Creation:
less than 1 day
Benefit Summary
To reduce fixture development time and resources required, Laser Design has provided solutions to many customers that include easy to use and accurate 3D measurement technology, paired with direct modeling software that anyone can use to design fixture geometry along with correcting CAD or creating 3D print ready files. In this case, we were able to provide a faster, better and less expensive option for our customer’s needs.
*Trademarks are owned by their respective companies.