Project
For a diabetic, there are few things more important than delivery of insulin at proper amounts and frequencies throughout the day. Many diabetics now use insulin pumps to automatically deliver both Basal and Bolus (background and mealtime) doses when needed to achieve the best control of their blood sugar levels. If the pump, or any component of the delivery process fails, the effect could be detrimental. For these reasons, it is imperative that all components in this process are inspected, and proper functioning is verified. In this case study, we will highlight inspection techniques focused on one component of this process, the insulin container. This container holds the insulin inside the pump and is critical for proper dose delivery once the pumping mechanism is engaged.
Challenges
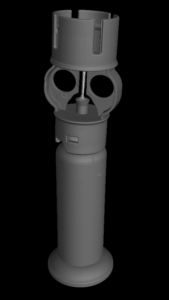
Full CT Scan Data of Container
When inspecting an assembly, it is important to inspect it in as close to a real-world scenario as possible. Testing the product without destroying it, and inspecting all components throughout the entire assembly at once are essential to getting the best results to guide downstream decisions. The insulin container assembly to be analyzed is made up of 6 total components; 5 of the parts are made of injection molded ABS plastic, and the needle at the center is made of stainless steel. The requirement is to measure the entire assembly without disassembling the parts so the stressed components can be analyzed in the constrained state. One of the key inspection points is the location of the needle and its orientation to other features of the assembly that support proper medication delivery.
Results
To accomplish the requirements of this inspection, the Laser Design services team determined that the 3D measurements needed could only be achieved using Computed Tomography (CT) technology which is available in the RX Solutions EasyTom CT Scanner. With this technology, 2D X-Ray images are captured at 1440 different positions around the insulin container assembly. These images are then reconstructed to create a 3D data set and the critical features can be extracted and measured.
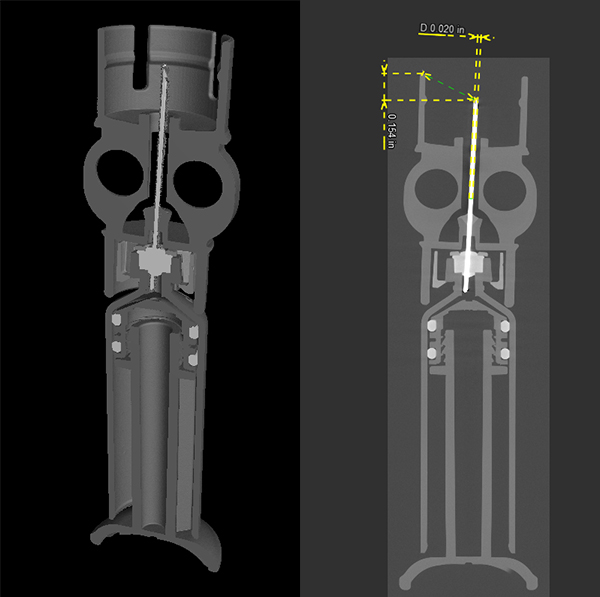
Cross Section and Cross Section with Diameter of Needle and Position
The highly trained Laser Design 3D scanning technician, with experience working a wide variety of projects, in many different industries, was able to narrow down the settings required to scan a multi-material assembly and provide quality 3D scan data. The 150kv x-ray source offered the best source voltage for this application, allowing appropriate penetration of the higher density materials along with capturing high resolution to define critical features with reliability. With this data, Laser Design engineers were able to measure and verify needle inner diameter, outer diameter and orientation to mating surfaces of the pumping mechanism that are imperative to successful insulin delivery processes.
Benefits
Using the EasyTom CT Scanner, along with Volume Graphics Studio Max software by Hexagon, the Laser Design team provided vital measurement data inside the insulin container assembly without destroying or disassembling the container. This data can be used to reliably make quick and effective decisions supporting product lifecycle goals. The project deliverables are made available through free viewer software so customers can communicate the results with many team members efficiently, further streamlining their processes.
Working with the Laser Design team, our customers get immediate access to trained and skilled resources providing 3D measurement results on an as-needed basis to accomplish immediate goals. When the time is right to bring these amazing 3D measurement technologies in-house, Laser Design and CyberOptics can help determine and provide the best overall 3D scanning, inspection and reverse engineering solutions that can achieve the best results for the application requirements.