Capturing both the internal and external geometries of small or complex parts is no easy task, but it can provide significant advantages for designers, engineers, and manufacturers across a variety of industries. Luckily, metrology-grade computed tomography (CT) offers a reliable, nondestructive method for capturing high-resolution 3D data of complex and free-form parts—without the need for line-of-sight visual access.
CT Scanning results include millions of data points that can be measured and analyzed to provide a number of key learnings. With the resulting measurements, engineers and designers can remove the external layer, dynamically section an assembly, and observe discreet distances between internal components. This method of 3D scanning is available in the form of 3D scanning services, which produce high-quality results with the help of trained operators.
If you’re searching for a service offering that can assist you with quality control, inspection, defect detection, and dimensional metrology, look no further. We’ve put together an overview of the technical capabilities and benefits of using industrial computed tomography technology for 3D measurement applications. Here’s what this advanced form of scanning can do for your complex parts or assemblies and how CT scanning can unlock valuable information that would otherwise be difficult, or impossible to measure.
10 Benefits and Uses of Industrial CT Scanning
1. Nondestructive Testing Method
In short, industrial CT scanning works by using radiographic technology to produce multiple 2D images of an object. As the object being scanned turns on a rotary table, x-rays penetrate it to varying degrees based on differences in density. The radiation that has not been absorbed by the part bounces back to a detector panel and produces hundreds of cross-sectional, 2D x-ray images that are then reconstructed to create the 3D measurement data.
There will be no cutting, slicing, stress, pressure, or other forces that could damage or otherwise affect the integrity of your part. This nondestructive aspect of industrial CT scanning makes it an excellent option for advanced analysis, quality inspection and reverse engineering for parts and assemblies with complex geometry and difficult to measure features.
2. Internal and External Measurement
Tactile CMM and non-contact laser and structured light measuring technologies have their place in recording form and dimension, but even they can’t deliver the internal and multi-material assembly details that a CT scanner can. CT scanning services will produce a complete 3D data set of both external and internal geometry, all without requiring line of sight or visual access to internal components.
That is perhaps the greatest benefit of industrial CT scanning—that it can be used to provide detailed internal measurements without the need to disassemble the part or product. The cross-sectional 2D images produced during a CT scan can be analyzed in addition to the constructed 3D model for a variety of metrology and inspection applications. Not only can this cut down on time-to-market, but it can also provide a method for efficient, simple quality control that might otherwise take an unrealistic amount of time or even leave flaws undetected.
3. Form Analysis
Yet another advantage of industrial computed tomography is that this inspection method allows for fast, accurate form analysis. CT scanning can be used to create a form analysis report comparing the accuracy of a physical part or assembly against a standard, such as a CAD file or a “golden” part. This comparison to a standard enables the detection of any deviations from technical specifications. Whether you’re in need of part to part, or part to CAD comparison, industrial CT scanning can provide access to features that can’t be measured in other ways at accuracies that rival tactile CMM measuring systems.
4. Dimensional Measurement and Reporting
Measuring and validating the internal geometries of complex parts can be challenging. While laser-based scanning and CMM technologies can record the external form and dimensions of a part, they require visual access in order to produce a representation of its inner dimensions. This may not be possible without compromising the structure or integrity of the part in question, and that risks skewing your measurements.
Fortunately, industrial CT scanning enables both internal and external dimensional measurement and reporting of an intact part. This makes computed tomography technology ideal for use with precise, injection-molded parts or other parts and assemblies with internal geometries that cannot be easily analyzed.
5. Wall Thickness Analysis
Wall thickness is another quality control element that can easily and quickly be analyzed with the help of industrial CT scanning. Minute variations in wall thickness throughout a part can interrupt the manufacturing or design processes and quickly become costly, especially if a manufacturer is producing a high volume of the same part. To detect any variations, a boundary is established around the external and internal features of a part. The distance between each surface is calculated to establish minimum wall thickness. Then the 3D data is rendered to illustrate the thickness values in color for quick visualization and easy interpretation. This method of wall thickness analysis does not require a nominal CAD file for comparison and is immensely valuable for detecting and remedying variations that might otherwise cause issues like cracking and distorted parts.
6. Defect Detection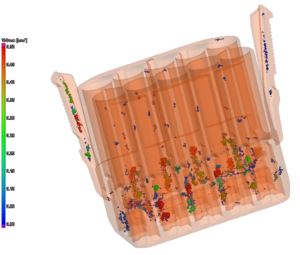
In addition to detecting dimensional flaws, industrial CT scanning also allows for the detection of manufacturing defects. This plays an essential role in both quality control and product development. CT scans can be used for porosity and inclusion verification, which involves identifying and pinpointing the position of areas of high and low density throughout a part. After the scan, the resulting model can be used to show the position and volume of both inclusions and internal pores, along with the percentages of porosity.
7. Fiber Flow Analysis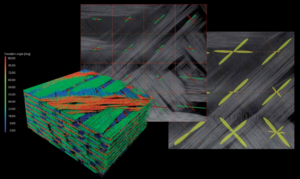
CT scanning is also useful for analyzing the orientation of embedded fibers used to reinforce materials like plastic. After an object is scanned, fiber flow analysis can reveal the direction in which the fibers are oriented at any point. From there, this measurement can be compared to the simulated nominal orientation of fibers. This type of analysis is useful for quality control and for creating a better understanding of how internal components in a composite material interact.
8. Failure Analysis
Failure analysis is a critical step in the product development cycle, and industrial computed tomography fits neatly into any arsenal of inspection and testing tools and technologies. Thanks to its nondestructive imaging method, CT scanning offers insights into a failed device or part that destructive testing methods can’t—without destroying the product and negating any subsequent tests. The high level of detail and accuracy provided by a CT scan offers a significant advantage when it comes to getting to the root cause of an issue.
9. Assembly Verification and Visualization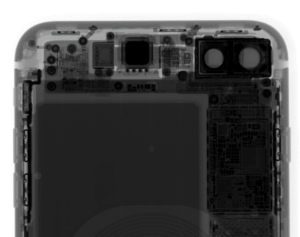
Before the introduction of computed tomography technology, validating and visualizing how various parts fit together in an assembly was difficult, if not impossible, without compromising the assembly. Instead of cutting into or otherwise disassembling the setup, we can now evaluate and measure the internal and external geometries of parts, as well as fit, through nondestructive CT scanning. This method can provide a number of valuable insights that will further inform product development and quality control efforts.
10. Research and Development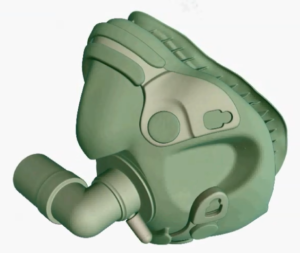
CT scanning also functions as an excellent tool for research and development purposes. Given the huge variety of analyses that can be performed with a single CT scan, this technology is ideal for universities, manufacturers, engineers, and product developers seeking further insight into material research, preliminary product designs or to make existing parts more efficient.
Industrial CT Scanning Services for Any Project
If you’re interested in incorporating industrial CT scanning into your project, contact Laser Design today. Our sales engineers will work to understand your project requirements and recommend the best solution. Then our trained technicians will complete the appropriate scan of your subject quickly and efficiently, delivering valuable data that meets your application goals. Whether you need a comprehensive understanding of internal parts for reverse engineering, comparison to CAD, dimensional analysis, defect detection or another application, we can help. Reach out if you have any questions about the scanning process or our services!