Laser Design 3D scanning engineers was to scan the entire electric car body, chassis, and components (rather than an assembly) to create a viable CAD model. Since the car didn’t exist as an assembly, Laser Design would not be able to create a reference scan from which the modelers could create the parts as perfectly matched components.
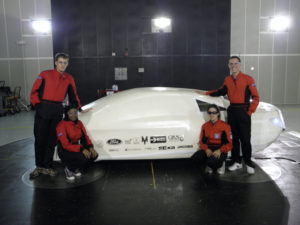
OLYMPUS DIGITAL CAMERA
The Organization:
The Massachusetts Institute of Technology (MIT) kicked off a project called the Vehicle Design Summit (VDS) which today has grown into a large international consortium of teams from universities and innovative companies seeking, amongst other pressing global needs dealing with energy and transportation, to develop a vehicle that dramatically reduces energy, materials, and toxics used in vehicles.
The Project:
As the initial focus, the VDS consortium is participating in the Automotive X PRIZE competition to design, build, and bring to market a hyper-efficient passenger vehicle earmarked for India that demonstrates a 95% reduction in energy use, materials and toxicity relative to the Prius.
The development team from MIT is entering a 4-passenger, optimized vehicle, the VDS Vision, into the competition in May 2010. They decided to use the Solectria Sunrise as a basis for their entry because the design is an extremely strong vehicular concept using all composite technologies and because the platform is now open source. Back in 1995 driving a prototype Solectria Sunrise, James Worden squeezed an amazing 375 miles out of one charge on 24 nickel metal hydride batteries. This long-distance record is unsurpassed to this day for an electric car with nearly the same interior space as a Ford Taurus. Also, the original Sunrise designer was an MIT alumnus which made the choice one of legacy as well. However, the existing prototypes were handmade, and as a result, surfaces were not completely regular and no CAD files existed.
The original Sunrise design had many good points: the longest all-electric car range on record, good aerodynamics, few body parts, and good crash test results. However, it also had some problems and flaws that the MIT team wanted to address. In order to improve and construct the car with modern automotive manufacturing techniques, it was critical that the team have a CAD model of the vehicle.
The advantage of using the Sunrise as their starting point was having a vehicle that had already met all the federal motor vehicle safety standards and was field tested, drastically reducing the development time. Because the design team consisted of students and faculty advisors, learning about high energy efficiency automotive design was one of the project goals, and the Sunrise provided a strong ecological framework to build upon.
Eventually, in addition to helping the MIT team create a lightweight energy-saving electric car to enter in the X PRIZE competition, a viable car kit of the model could also be developed from the scan data. This car could use composite technology to produce an electric car supported by available aftermarket components for the Mercury Cougar. The lightweight improvements which will lengthen the achievable distance on a single battery charge will be incorporated into the vehicle components using the current Metro suspension and basic design.
From MIT’s perspective, an accurate CAD model of the existing vehicle was needed to work on redesigning features, analysis, and testing. The vehicle from which they were working happened to be located in Minnesota, near Laser Design, a leading provider of 3D laser scanning, dimensional inspection, long range scanning, and CT scanning services for over 25 years. The project director at MIT contacted Larry Carlberg, Service Bureau Manager about 3D laser scanning the car components and modeling them into a smooth non-parametric model. Because Laser Design is supportive of the energy saving research efforts of this MIT initiative, Carlberg agreed to waive the 3D modeling fee.
Carlberg noted, “When I was first contacted regarding this scanning job, I knew very little about the scope and objectives of the X PRIZE project. We saw images of some of the parts and quoted scanning and modeling a chassis, body, door, hood, and trunk of the Solectria Sunrise to be used by the MIT development team. We have done similar work for companies like Polaris, John Deere, and many other automotive related manufacturers, so we guarantee optimal results. This project was ideally suited to scanning and reverse engineering into appropriate Solidworks CAD models.”
The Challenge:
The challenge for the Laser Design scanning engineers was to scan the entire Sunrise body, chassis, and components (rather than an assembly) to create a viable CAD model. Since the car didn’t exist as an assembly, Laser Design would not be able to create a reference scan from which the modelers could create the parts as perfectly matched components. However, they could use the available parts to create a smooth, symmetrical model and remove the handmade errors so everything could fit together correctly. Some items, such as the doors, would be mirrored to insure symmetry. Having a CAD model would enable the MIT design team to create their desired changes quickly.
Non-contact 3D laser scanning is a complete measurement method; it captures everything on the surface of an object, including free-form shapes and fine details. The technology works by projecting a line of laser light onto a surface while cameras continuously triangulate the changing distance and profile of the laser line as it sweeps along. The laser line passes back and forth over the area until the complete surface is captured. Irregular shapes are measured just as easily as prismatic ones, and they are instantaneously replicated digitally on-screen. The scanner measures very quickly, picking up tens of thousands of points per second, and generates huge numbers of data coordinates in a point cloud. If the object or objects are large, such as in the case of a car, several scans are made to capture the entire part and then the point cloud data files are rotated into the same reference frame and assembled into an exact 360-degree 3D model of the scanned part.
Since laser scanning is a non-contact measuring method, there are no variations in practices or techniques from operator to operator, or pressure differences that may generate different readings in traditional touch-probe measurement. Laser scanning allows extremely consistent capturing of parts’ geometry by removing the human error factor.
The MIT team will use these part scans as a starting point in developing their X PRIZE entry. They realize the limitations and strengths of using the Sunrise parts and will use them to their advantage in the new design.
The Solution:
Laser Design worked with the MIT team to scan the disassembled Sunrise components with both their advantageous and challenging characteristics. Scanning accuracy required for the body surfaces was ± 1 cm; for interfaces, it was ± 1 mm. Laser Design engineers scanned the following Sunrise body parts:
- body
- chassis
- passenger door
- rear window surround (the part of the body that the plastic window sat in)
- lower edge of rear window where center brake light was mounted
- rear seat (rear bulkhead, which forms the seat backs and shelf under the rear window)
- rear bumper with taillight buckets
- hood
- mold for trunk lid
- right rear fender
- left rear fender
- front bumper (a urethane fascia)
- battery tunnel
After the point cloud data was collected from the scanning process, Laser Design engineers quickly converted it into polygon models, commonly referred to as STL models. From the STL models, Laser Design extracted evenly spaced cross sections through the model and exported them as IGES curves. These curves can be used by MIT CAD engineers to make changes in the models, or they can be used by manufacturers in CAM to cut templates for the development of composite components, such as developing lightweight, yet very strong wings in aerospace kits. This technology could also be employed to develop the Sunrise kit.
The data was converted into a non-Class A non-parametric model in SolidWorks for reverse engineering. Accuracies were reduced by the modeling process to create a CAD model that fit together well. This model has all the features defined on the Sunrise as it exists, but also incorporated the improvements needed to create a symmetrical model. Much of the hand-work anomaly was removed, but a “perfect” fit was not possible since Laser Design did not have an assembly scan as a baseline reference model.
The SolidWorks export models were to be made symmetrical unless otherwise specified or obviously asymmetrical in the scanning. For example, a single door was scanned and mirrored to create the other door. All components were scanned, some on both sides. Some parts needed to be scanned as an assembly to build a reference model which ensured correct alignment of the components. Since the original Sunrise body did not supply exact locations for the hinges, latches, or weatherstripping interfaces between the body and the door, it was important that Laser Design provide models that presented information to MIT to improve the CAD models.
The Results:
Scanning the body, chassis, and the other 11 handmade components took about 30 hours. The modeling phase was somewhat longer, another 80 hours, because the Laser Design modelers were not just modeling the scan data in the condition it was collected. Rather they were incorporating corrective measures through an iterative process so that all the parts would fit together correctly. The scan data as collected was the reference that could be referred back to, and from which a smooth, symmetrical model was created. The asymmetries of the original handmade components were corrected and streamlined, so that the MIT team could use the CAD model as a starting point to design their improvements in structure, such as a more aerodynamic shape to reduce wind resistance, and lighter components so more batteries could be added without adversely affecting distance capability.
The CAD models were delivered as they were completed. Total project time, start to finish, was about two weeks, an amazing turnaround time considering the large scale of the project, number of parts, and advanced modeling required. Models were delivered through email download links which can easily be forwarded to all parties involved. The quick turnaround reflected a meeting deadline with a key advisor to go over and update the design. At that time the MIT team needed all the original Sunrise components.
The MIT team will develop the unibody structure with advanced composite materials that incorporate the required strength without adding unwanted weight. Because the underlying structure will be lighter, it will be able to carry more batteries to get the maximum travel on one charge. The modified rear and back bumper of the Sunrise will become a hatchback style for less wind resistance and the ability to haul cargo. Other improved components will be mostly developed in-house which will require various design changes all accomplished through the CAD model developed by Laser Design’s laser scanning and 3D modeling expertise.
All of the lessons learned in the development process and new technologies advanced by the MIT team will lead directly to other “green” automotive applications and designs. The CAD world opens doors to theoretical testing and practical improvements in the world of transportation. The X PRIZE competition entry from the MIT team will be built by the end of January 2010. The project director commented, “We would never be able to get there without laser scanning and the CAD models produced by Laser Design.”